Blow Molding
Our blow molding process produces custom prototypes and end-use production parts in 15 days or less. We use aluminum molds that offer cost-efficient tooling and accelerated manufacturing cycles, and stock more than 100 different thermoplastic resins.
How Does Plastic Blow Molding Work?
Blow molding, also called blow forming, is a manufacturing process that is conducted by using thermoplastics by which hollow plastic profiles are formed. Blow molding process at BEPL begins with applying heat energy to the thermoplastic resins thus which converts them into a molten state and forming them into a parison or perform.
The parson is a tubular piece of plastic with a hole in one end in which compressed air is released. The compressed air expands the parson into the female mold cavity, while the pressure of the compressed air is maintained for a predetermined period of time, thus allowing the parison to expand and take the shape of the mold cavity. Once the plastic has cooled the mold is opened and the part is ejected.
Watch: How Blow Molding Works
See this example of making pet bottles using a blow molding machine.
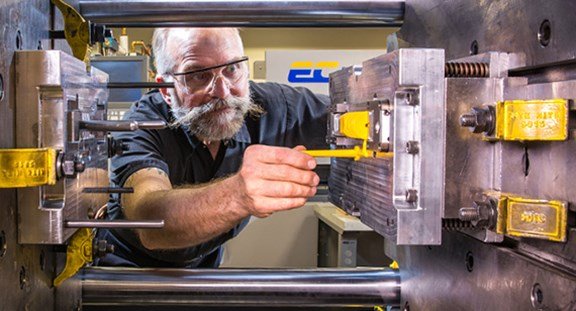
Molding Options: Prototyping or On-demand Manufacturing?
Consider part quantities, lifetime maintenance, level of inspection, and cost when determining which option is right for blow molding.
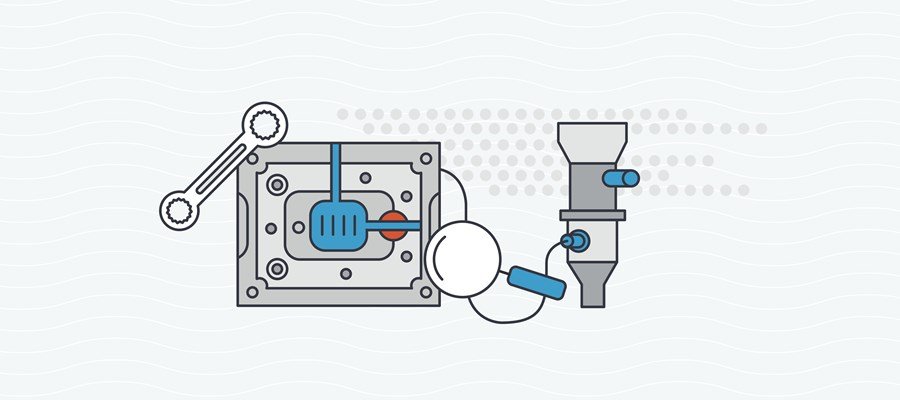
Design Guidelines
VIEW GUIDELINES >
Thermoplastic Materials
Choose from production-grade thermoplastic resins ranging from ABS, PP, PC and nylon to high-performance resins like PEEK and PEI. A number of colorant options are available and customer-supplied thermoplastics are also accepted.
VIEW MATERIALS
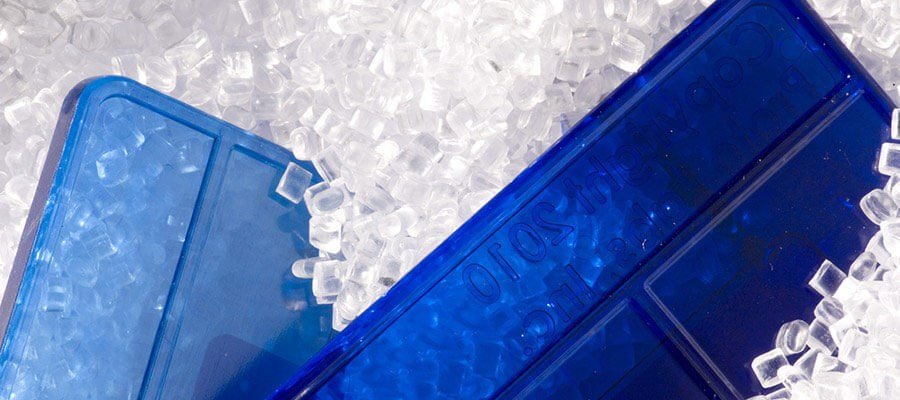
RESOURCES
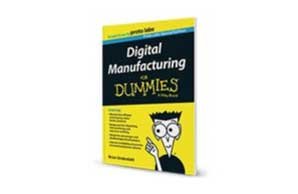
Digital Manufacturing for Dummies
Compare the various 3D printing , CNC machining, and injection molding technologies and learn how to leverage each process to get the products to market fast.
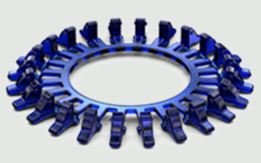
Designing for Moldability: Fundamental Elements
Learn what product designers must consider when designing a part for injection molding, including:warp surface finish, stress, resin additives, and more.
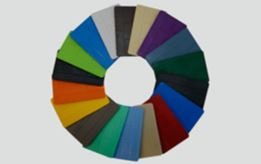
How to Choose the Right Thermoplastic
In this webinar, we examine material properties and provide guidelines to help you choose the right thermoplastic material for your application.
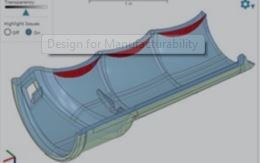
Design for Maufacturability
View an injection molding sample quote to experience BEPL quotes free analysis.